In a recent development AIRIA Southern Region along with the IRMRI has inaugurated a Tech Series which will tap on to subjects like innovation, partnerships, enhance standards and quality and build operational efficiencies. Further, with the growth of infrastructure projects and auto industry in India, a huge demand can be anticipated for the rubber products industry, tyres, specialty rubber products etc. which the Series tends to bring to the foreground and equip industry in a timely fashion as an enabler.
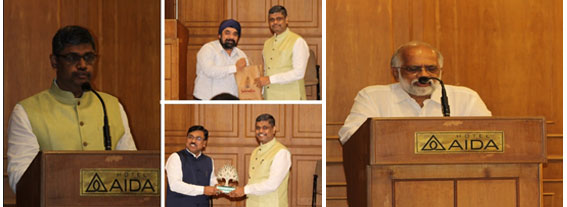
Mr. Rajagopal, Director of Ceyenar Chemicals, AIRIA Management Committee, welcomed the attendees and the esteemed speakers at the inaugural ceremony in the august presence of the Chief Guest, M Vasanthagesan, IRS, Executive Director, Rubber Board. He highlighted the significance of technological innovation that pushes the boundaries of what is possible in the rubber industry to enhance standards and operational efficiencies. He also added how Ceyenar supports the rubber industry with polymers and chemicals.
The Chief Guest, M. Vasanthagesan, IRS, Executive Director, Rubber Board, highlighted the significant milestone in the industry’s adaptation to digital technologies allowing for easy and efficient authentication of certificate details. He dwelled on utilizing untapped rubber plantations by training tappers and fostering local partnerships to harness rubber resources and bolster economic development in partnership with the tyre industry.
Dr. Rajkumar interacted with rubber growers and processors in his session on Basic Rubber Compounding and Cost Reduction. He outlined that rubber can be deformed to a high degree of strain in a reversible manner and this finds use in fields as diverse as transportation, material handling, health care, and sport and leisure activities. In order to understand. the complex, multidisciplinary science of selecting and blending the appropriate combination of elastomers and other ingredients to meet the performance, manufacturing, environmental, and cost requirements for rubber goods, one must have familiarity with raw materials, their physical forms, functions in the compound, and behaviour during processing. Economic factors play a big role in arriving at the optimum mixing-masticating of the elastomer to make it receptive to other ingredients while retaining sufficient stiffness to ensure adequate dispersion. Starting from a simplest of all compounds, rubber plus vulcanizing agent, he stated one has to consider how it can be compounded with reinforcing agents, antioxidants, and plasticizers to give the best combination of properties for a particular application. The mechanism of specifying the type and amount of various ingredients in a mix, the manner of mixing, the processing of the mixed compound, and the method and details of vulcanization based on the end-use and service properties, processability, and cost. One should design a compound connected with the choice of rubber, the level of reinforcement, and type of vulcanization system to be employed. These determine cost, mechanical and visco elastic properties, resistance to degrading influences, processability, and special requirements such as flame resistant, low temperature flexibility and non-toxicity applications. He also touched upon the physical tests of quality to measure physical properties and attributes of the rubber compound that is often connected to product design and manufacturing. There was enough discussed on the compound properties desired for different rubber compounds for tyres, retreading materials, conveyor belting, transmission belting, hose, footwear, medical applications, O rings, and seals. With regard to cost reduction, Dr. Rajkumar covered cost cutting as a driving force and associated economic considerations. This included overhead cost reduction, rubber product quality cost, cost comparison between molded rubber and TPV parts, material cost reduction in rubber processing, cost reduction in the rubber mixing room, cost reduction via rubber compound filtration, contribution of injection molding machines to cost reduction, process cost reductio in rubber injection molding, cost improvement potentials in tyre manufacturing mixing plant, reduction in processing cost and other cost saving thoughts. Dr. Rajkumar concluded that the market for rubber processing and compounding is positive, with increasing demand for high-performance and environmentally sustainable rubber products. Key trends driving this growth include a growing demand for electric vehicles, advancements in tyre technology, and increased demand for rubber products in emerging markets. The focus on sustainability and reducing carbon footprint see many companies investing in research and development to develop sustainable rubber products.
Dr. Siby Varghese, Joint Director, Rubber Research Institute of India started the next session on Trouble Shooting in Rubber Compounding Process according to the type of rubber involved. He began by stating that problems with rubber are to be expected considering the complexity of the many materials, processing, design, and testing steps. The problems that occur vary substantially from one factory to another and can include materials including rubber, chemicals, fillers, steel wire etc., mixers, mixed rubber compound, shaping operations, vulcanizing, post vulcanization and testing and quality assurance. Examples such as cold flow of polymers in the receiving area, mixing problems, mix quality, dispersion, stickiness, extrusion die swell, extrudate appearance, calendaring blisters, release from rolls, and molding release, nonfills, and porosity were outlined. Dr. Varghese stated that the problems can and do happen during these steps, either singularly or in combination. Rubber products are basically systems involving three main factors - material, process and design. These three factors are often interactive. So it is important to consider both compound and design and view the manufacture of a rubber product as a system. He stated that overemphasis on materials considerations to the exclusion of processing factors can be problematic. Use experiment design judiciously and significantly reduce rubber scrap rates. He concluded by stating that a compound should not only be designed for its specification properties at an acceptable cost, but it must process with minimum problems through factory operations. Therefore he stressed on factors to use as a checklist - solve root causes of problems, make effective use of consultants, and provide employee training. On identifying the cause of any process defect, he stressed considering human factor inconsistent cycle time can cause issues with material temperature and residence time variations that contribute to mold temperature inconsistencies, lost productivity, and increased scrap rate; machine functions method of process set up; mold and material.
Session 3 was by Mr. Gaurav Somwanshi, CEO of Emertech Innovations on a view on European Deforestation Regulations for European Exporters. It is an year since a key building block in the fight against climate change and biodiversity loss, entered into force. This law ensures that a set of key goods exported to the EU market is deforestation free and will no longer contribute to deforestation and forest degradation in the EU and elsewhere in the world. One should confirm that the product has been produced on land that has not been subject to deforestation or forest degradation after December 31, 2020. One should conduct strict due diligence if they export on the EU market rubber and derived products. This in turn reduces greenhouse gas emissions and biodiversity loss. It is the onus on producers to engage in sustainable production processes and improve supply chain transparency. One should enhance trade in deforestation free products and boost opportunities for sustainable actors around the world. Deforestation and forest degradation are important drivers of climate change and biodiversity loss. Therefore halting deforestation and restoring ecosystems is the most effective way to bring down CO2 levels after rapid deployment of wind and solar energy. One can continue selling your commodities in the EU provided you can prove that the products produced are deforestation free. He also added that the collaboration with IRMRI harnessed cutting edge blockchain technology to enhance the standards and verifiability of credentials by ensuring transparency and trust in digital transactions.
The concluding interactive session, the question &answer session, saw panel members Dr. K. Rajkumar, Dr. Siby Varghese and Mr. A. Samad, respond to questions posed by rubber producers, growers and processors.
The Vote of Thanks was given by Shri Raja Annamalai M - Regional Committee and also emphasized for joining AIRIA Southern Region Chennai.